一般来说只要有在
SMT生产打滚过的工程师,他们大多不喜欢生产有双面BGA设计的PCB,因为板子上有BGA的存在本身就已经不太容易生产了,而双面都有BGA设计的板子又比只有单面BGA设计的PCB更容易产生不良品。
有不良品就意味着有无穷无尽的改善得做,而且BGA重工通常费时又费劲,重工后还不一定就可用,你说有那个SMT工程师犯傻了。
那为什么双面BGA的PCB较容易出现不良品呢?
正常情况BGA零件通常会被安排在第二面才过Reflow,这是为了避免第一面Reflow的缺点在第二面Reflow时被放大,这些缺点包含BGA焊球孔洞(void)比率增加、HIP或WNO空假焊比率增加、焊点脆化、BGA零件掉落等主要问题,次要问题是双面BGA的板子维修不易。
二次回焊后BGA焊球孔洞(void)比率增加
一般认为是这因为二次回焊时,BGA锡球可能重新熔融,让原本散布于BGA内的许多细小孔洞(micro-void)有机会重新聚集成为一个较大的孔洞(void),当锡球的Void越大,就表示锡球的可靠性越差,IPC-7095内有规定孔洞不得大于一定的百分比,因为一旦产品受到落下、振动等外力影响时有孔洞的锡球断裂机率就越高。
BGA锡球的孔洞(void)可不仅仅是那些肉眼可以看到的而已,有专家针对BGA锡球的孔洞分成了下列几类:
▪ Marco Voids:锡膏中助焊剂所行程的孔洞。
▪ Planar Micro-voids:一般出现于SMD(Solder-Mask-Defined)的板子,因为锡膏有机会印刷于防焊层,防焊层与焊垫之间的高度差与防焊表面粗糙度所形成的孔洞。
▪ Shrinkage Voids:锡球外壁的小洞。
▪ Micro-Via Voids:焊垫/焊盘上via形成的孔洞。
▪ IMC Micro-voids:IMC层长时间或多次热循环后老化形成于IMC附近的孔洞。
▪ Pinhole Micro-voids:这类孔洞一般出现在IMC层,由电路板上金属层原本的细小孔洞所形成。
相关阅读:
目前应该是无法完全避免BGA锡球孔洞(voids)的发生,不过可以在回焊炉内加氮气(N2)来增加焊锡的润湿性并降低锡球孔洞的发生率。
二次回焊后,焊点脆化,承受落摔能力变差
这个应该是属于信赖度的问题,而且属于不可逆的反应,更甚的这一般在制造工厂是测试不出来的。
这是因为每经过一次Reflow就是对焊锡的再一次加热,而每一次的加热都会让IMC层变得更厚,也就是老化,铜基地的IMC (InterMetallic Compound) 还会从原本的良性Cu6Sn5转变为劣性的Cu3Sn。不论是哪种金属基地的PCB,当IMC变得越来越厚,就表示焊锡变得越脆,也越无法承受落下时的冲击力。
可以把IMC想像成砖块间的水泥,不同的砖块分属不同的金属,其间必须形成类似水泥的IMC才能互相连接在一起,如果水泥层越厚(IMC层越厚),当砖块承受到推拉应力时,就越容易从水泥层断裂,在焊接中就是IMC层。
BGA零件于第二面回焊时掉落的风险
正常情况下打在第一面的BGA零件应该不至于在第二面过炉时掉落到回焊炉内的,深圳宏力捷打过ARM CPU也没有掉件过,不过如果有重量比较重的BGA就难说了。
不过看网络上偶尔还是会有网友会提问,如果有看文的朋友有实际发生的案例可以提出来一起讨论。
相关阅读:
如果无法避免双面BGA的设计出现,那有没有什么比较好的建议可以降低其风险呢?
老实说深圳宏力捷还未发现有这方面的工业标淮,不过根据以上篇幅说明双面BGA的缺点,深圳宏力捷有以下的建议:
▪ 尽可能少放BGA零件于第一面Reflow。
▪ 将重量比较轻、尺寸比较小、锡球pitch比较大的BGA设置在第一面。
▪ 将比较重要的BGA零件(如CPU)设置在第二面Reflow。
▪ 尽量不要将BGA零件设置于PCB的正中心,因为正中心通常是PCB变形最严重的位置。
深圳宏力捷推荐服务:PCB设计打样 | PCB抄板打样 | PCB打样&批量生产 | PCBA代工代料
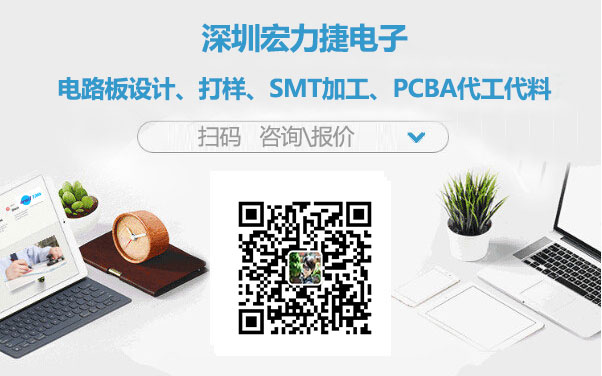