对电子产品设计师尤其是
线路板设计人员来说,产品的可制造性(制程性)是一个必须要考虑的因素,如果线路板设计不符合可制造性(制程性)要求,将大大降低产品的生产效率,严重的情况下甚至会导致所设计的产品根本无法制造出来。
如今的用户要求产品价格更低、品质更高同时交货期更短,有一种工具可同时满足这三个目标,这就是可制造性设计,也称为DFM。和在其它行业中一样,DFM在印刷电路板装配PCBA中也是同样适用并且非常重要的。
图1:具有较高引脚数的元件应使用椭圆形焊盘以防止波峰焊时出现锡桥。
什么是DFM?在《加工与制造工程师手册》(Tool and Manufacturing Engineers Handbook)一书中作者William H. Cubberly和Raman Bakerjian对此作了如下解释:“DFM主要研究产品本身的物理设计与制造系统各部份之间的相互关系,并把它用于产品设计中以便将整个制造系统融合在一起进行总体最佳化。DFM可以降低产品的开发周期和成本,使之能更顺利地投入生产。”
众所周知,设计阶段决定了一个产品80%的制造成本,同样,许多品质特性也是在设计时就固定下来,因此在设计过程中考虑制造因素是很重要的,而且这些都应该让设计人员知道。若想提高效率,各公司应有自己的一套DFM,并对其进行分类和维护,DFM文件应该是随环境条件变化而改变的动态性文件,它由一个核心委员会进行管理,委员会成员至少要包括设计、制造、市场和财务等部门的人员。
通孔插装技术如今仍然在使用,DFM在提高通孔插装制造的效率和可靠性方面可以起到很大作用,DFM方法能有助于通孔插装制造商降低缺陷并保持竞争力。本文介绍一些和通孔插装有关的DFM方法,这些原则从本质上来讲具有普遍性,但不一定在任何情况下都适用,不过对于与通孔插装技术打交道的PCB设计人员和工程师来说还是有一定的帮助。
读者也可以用这些原则作为DFM文件的框架,然后在其中加入自己具体的设备配置及冗余量要求。这些原则可以帮助工程师以一种更专业的态度做决定,使他们尽快成熟。
下面列出的各条原则根据制程进行编号和分类以便于查询。
排版与布局
在设计阶段排版得当可避免很多制造过程中的麻烦。
1.用大的板子可以节约材料,但由于翘曲和重量原因它在生产中输运会比较困难,它需要用特殊的夹具进行固定,因此应尽量避免使用大于23×30cm的板面。最好是将所有板子的尺寸控制在两三种之内,这样有助于在产品更换时缩短调整导轨、重新摆放条形码阅读器位置等所引致的停机时间,而且板面尺寸种类少还可以减少波峰焊温度曲线的数量。
2.在一个板子?包含不同种拼板是一个不错的设计方法,但只有那些最终做到一个产品?并具有相同生产制程要求的板才能这样设计。
图2:元件的排列若不是0度或90度将造成机器插装困难。
3.在板子的周围应提供一些边框,尤其在板边缘有元件时,大多数自动装配设备要求板边至少要预留6mm的区域。
4.尽量在板子的顶面(元件面)进行布线,线路板底面(焊接面)容易受到损坏。不要在靠近板子边缘的地方布线,因为生产过程中都是通过板边进行抓持,边上的线路会被波峰焊设备的卡爪或边框传送器损坏。
5.对于具有较高引脚数的元件如接线座或扁平电缆,应使用椭圆形焊盘而不是圆形以防止波峰焊时出现锡桥(图1)。
6.尽可能使定位孔间距及其与元件之间的距离大一些,并根据插装设备对其尺寸进行标淮化和最佳化处理;不要对定位孔做电镀,因为电镀孔的直径很难控制。
7.尽量使定位孔也作为PCB在最终产品中的黏着孔使用,这样可减少制作时的钻孔工序。
8.可在板子的废边上安排测试电路图样(如IPC-B-25梳形图案)以便进行制程控制,在制造过程中可使用该图样监测表面绝缘阻抗、清洁度及可焊性等等。
9.对于较大的板子,应在中心留出一条通路以便过波峰焊时在中心位置对线路板进行支撑,防止板子下垂和焊锡溅射,有助于板面焊接一致。
10.在排版设计时应考虑针床可测性问题,可以用平面焊盘(无引线)以便在线测试时与引脚的连接更好,使所有电路节点均可测试。
元件的定位与安放
11.按照一个栅格图样位置以行和列的形式安排元件,所有轴向元件应相互平行,这样轴向插装机在插装时就不需要旋转PCB,因为不必要的转动和行动会大幅降低插装机的速度。像图2上这些45度角元件实际上无法由机器插入。
12.相似的元件在板面上应以相同的方式排放。例如使所有径向电容的负极朝向板件的右面,使所有双列直插封装(DIP)的缺口标记面向同一方向等等,这样可以加快插装的速度并更易于发现错误。如图3所示,由于A板采用了这种方法,所以能很容易地找到反向电容器,而B板查找则需要用较多时间。实际上一个公司可以对其制造的所有线路板元件方向进行标淮化处理,某些板子的布局可能不一定允许这样做,但这应该是一个努力的方向。
13.将双列直插封装元件、连接器及其它高引脚数元件的排列方向与过波峰焊的方向垂直,这样可以减少元件引脚之间的锡桥。
图3:所有径向电容的负极朝向一边可很容易发现错误(A),反之则较为困难(B)。
14.充分利用丝印在板面上作记号,例如画一个框用于贴条形码,印上一个箭头表示板子过波峰焊的方向,用虚线描出底面元件轮廓(这样板子只需进行一次丝印即可)等等。
15.画出元件参考符(CRD)以及极性指示,并在元件插入后仍然可见,这在检查和故障排除时很有帮助,并且也是一个很好的维护性工作。
16.元件离板边缘应至少有1.5mm(最好为3mm)的距离,这将使线路板更加易于进行传送和波峰焊接,且对周边元件的损坏更小。
17.元件高出板面距离需超过2mm时(如发光二极体、大功率电阻器等),其下面应加垫片。如果没有垫片,这些元件在传送时会被“压扁”,并且在使用中容易受到震动和衝击的影响。
18.避免在PCB两面均安放元件,因为这会大幅增加装配的人工和时间。如果元件必须放在底面,则应使其物理上尽量靠近以便一次完成防焊胶带的遮蔽与剥离作业。
19.尽量使元件均匀地分布在PCB上,以降低翘曲并有助于使其在过波峰焊时热量分布均匀。
机器插装
20.所有板上元件的焊盘都应该是标淮的,应使用业界标淮的间隔距离。
21.选用的元件应适用于机器插装,要牢记自己工厂内的设备的条件与规格,事先考虑好元件的封装形式以便能更好地与机器配合。对于异型元件来讲,封装可能是一个较大的问题。
22.如果可能,径向元件尽量用其轴向型,因为轴向元件的插装成本比较低,如果空间非常宝贵,也可以优先选用径向件。
23.如果板面上仅有少量的轴向元件,则应将它们全部转换为径向型,反之亦然,这样可完全省掉一种插装工序。
24.布置板面时应从最小电气间隔的角度考虑引脚折弯方向和自动插装机元件所到达的范围,同时还要确保引脚折弯方向不会导致出现锡桥。
导线与连接器
25.不要将导线或电缆线直接接到PCB上,而应使用连接器。如果导线一定要直接焊到板子上,则导线末端要用一个导线对板子的端子进行端接。从线路板连出的导线应集中于板子的某个区域,这样可以将它们套在一起避免影响其它元件。
26.使用不同颜色的导线以防止装配过程中出现错误,各公司可采用自己的一套颜色方案,如所有产品数据线的高位用蓝色表示而低位用黄色表示等。
27.连接器应有较大焊盘以提供更好的机械连接,高引脚数连接器的引线应有倒角以便能更容易地插入。
28.避免使用双列直插式封装插座,它除了延长组装时间外,这种额外的机械连接还会降低长期使用可靠性,只有因为维护的原因需要DIP现场更换时才使用插座。如今DIP的品质已取得了长足的进步,无需经常更换。
29.应在板面上刻出辨别方向的标记,防止黏着连接器时出现错误。连接器焊点处是机械应力较为集中的地方,因此建议使用一些夹持工具,例如键和卡扣。
整机系统
30.应在设计印刷电路板前选好零配件,这样可以实现最佳布局并且有助于实施本文中所阐述的DFM原则。
31.避免用一些需要机器压力的零元件,如导线别针、铆钉等,除了黏着速度慢以外,这些元件还可能损坏线路板,而且它们的维护性也很低。
32.采用下面的方法,尽量减少板上使用元件的种类:
‧用排电阻代替单个电阻。
‧用一个六针连接器取代两个三针连接器。
‧如果两个元件的值很相似,但公差不同,则两个位置均使用公差较低的那一个。
‧使用相同的螺钉固定板上各种散热器。
33.最好设计成可在现场进行配置的通用板。例如装一个开关将国内使用的板改为出口型号,或使用跳线将一种型号转变为另一型号。
常规要求
34.当对线路板做敷形涂层时,不需要涂层的部份应在工程设计时在图上标注出来,设计时应考虑涂层对线间电容的影响。
35.对于通孔来说,为了保証焊接效果最佳,引脚与孔径的缝隙应在0.25mm到0.70mm之间。较大的孔径对机器插装有利,而想要得到好的毛细效果则要求有较小的孔径,因此需要在这两者之间取得一个平衡。
36.应选用根据工业标淮进行过预处理的元件。元件淮备是生产过程中效率最低的部份之一,除了增添额外的工序(相应带来了静电损坏风险并使交货期延长),它还增加了出错的机会。
37.应对购买的大多数手工插装元件定出规格,使线路板焊接面上的引线伸出长度不超过1.5mm,这样可减少元件淮备和引脚修整的工作量,而且板子也能更好地通过波峰焊设备。
38.避免使用卡扣黏着较小的座架和散热器,因为这样速度很慢且需要工具,应尽量使用套管、塑料快接铆钉、双面热带或者利用焊点进行机械连接。
本文结论
对于用通孔插装技术进行线路板组装的制造商来说,DFM是一个极为有用的工具,它可节约大量费用并减少很多麻烦。使用DFM方法能减少工程更改以及将来在设计上作出让步,这些好处都是非常直接的。希望本文介绍的这些原则能帮助通孔线路板设计工程师和上层管理人员对制造的状况有个更清楚的了解,并促进相互之间有更好的交流。
深圳宏力捷推荐服务:PCB设计打样 | PCB抄板打样 | PCB打样&批量生产 | PCBA代工代料
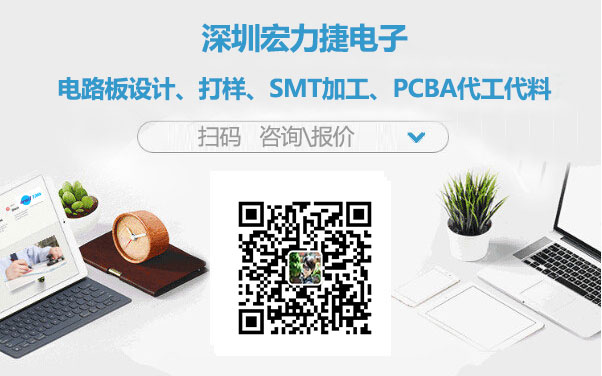