晶片级封装(CSP)已成为面阵列封装设计的主要方式,利用其小巧的面积和格栅阵列技术能够做出更小、更快、更便宜的零组件,用于记忆体、电信及多媒体等多种应用中。但CSP技术的出现却给后端制程带来了新的难题,
PCBA制造商们必须要仔细考虑制程流程的参数,才能使做出的产品在良率和可靠性等方面满足应用的要求。
EEMS
目前市面上的CSP元件类型数以百计,其中Tessera公司设计的μBGA已逐渐成为市场主流之一,已有多家整合电路PCBA制造商和组装厂商获得该项设计的使用授权。μBGA封装结构设计灵活,可避免晶片与印刷电路板(PCB)间因热膨胀不匹配而带来可靠性问题,其小巧、轻便、薄型封装设计非常适用于可携式产品和其它空间狭小的应用中。
然而使要成功运用这类设计,对制造来说却是一种挑战。CSP技术的出现为后端制程带来了新的难题,同时由于终端产品市场固有的成本驱动特性,它还增加了PCBA制造商在产量和产能上的压力,这些难题与压力促进了高速高良率自动化焊球贴装制程需求的成长。
1999年意大利一家独立的半导体记忆体装配和测试机构EEMS在自己的工厂着手开始组装CSP,装配的产品采用Tessera的μBGA封装,组装时对焊球贴装制程各方面进行了重点考察,包括焊盘形状、基板载带、焊球贴放、助焊剂发配以及晶片的运送等。为了解决生产难题,EEMS委託美国Robotic Vision Systems公司的Vanguard事业部安装了一条完整的焊球贴装线,其中包括VAi 6300自动焊球贴放系统、回流焊炉、回流焊后的清洗机和材料运送设备(图1)。
独特的焊盘形状
EEMS的μBGA焊盘形状为焊球贴装带来了很多难题,它的焊盘在基板载带表面下方凹入0.069mm(图2),这样在用标淮感光剂丝网进行焊锡助焊剂印刷时,很难控制助焊剂的用量和避免助焊剂桥接。
凹入的焊盘再加上焊盘直径特别小(0.33mm),使得对焊球贴放的淮确度要求远远高于标淮应用。普通焊盘设计允许贴放位置出现偏差,因为轻微偏离的焊球在焊锡回焊时能自行对中到焊盘上;而对于EEMS封装来说,位置偏移的焊球不会与焊盘或助焊剂接触,它错过了焊盘所在的小“口袋”,因此无法利用焊球、助焊剂和焊盘之间的附着力特性,结果这个焊盘将漏掉焊球,最终产生不完全回流焊而少一个I/O连接。
载带式基板
采用载带设计的引脚框组件需对焊球贴装制程有一些独特的考虑。封装排列在载带基板上,载带基板本身又固定在引脚框上,由于基板载带具有柔韧性,因此最好是在载带上安排一些孔以便于机械对位。但在EEMS应用中这却无法做到,所以将孔留在引脚框上是组装定位的唯一可选方法。组装过程中基板载带可能会伸长,使得引脚框和载带基板之间误差产生累积,从而增加了对助焊剂发配和焊球贴放制程精度的要求。由于焊球贴放系统依靠引脚框来进行定位,所以这些制程必须保持很高的精度以克服因载带弯曲而可能产生的焊盘位移。
除了前面提到的焊盘形状问题之外,由于在引脚框上固定基板载带的黏着带位于焊盘表面上方,所以传统的助焊剂丝印方法也有困难,刮刀将与黏着带而不是焊盘接触,导致助焊剂用量不均匀。
裸晶片运送
Tessera的μBGA封装采用的是裸晶片,没有用密封剂或模塑保护,如果不仔细运送或固定元件很容易损坏。为了将这种损坏的风险降到最低,材料的运送在焊球贴装线每个阶段都很重要。
整合解决方案
对封装制程最初的分析显示,需要一个助焊剂发配和焊球贴放都有很高精度的高产量解决方案,为了得到可靠的高良率焊球贴装,整个生产线必须考虑封装对每一步制程的要求。通过客户和供应商工程力量的共同协作来满足这些要求,研究重点主要是助焊剂发配、焊球贴放、定位夹具以及元件运送等几个方面。
◆助焊剂发配
由于黏着载带和焊盘形状的原因而无法使用感光剂丝印来涂覆助焊剂,因此这选用了一种刚性助焊剂漏板(RFS)技术,该技术可以使VAi 6300焊球贴放系统为焊球贴装所需的细间距助焊剂发配提供一个更加精确均匀的方法。对于这的应用来说,RFS主要解决封装位置精确一致、避免助焊剂桥接、助焊剂一致性以及基板上有黏着载带时的助焊剂处理能力等几个方面。
RFS用铝合金制造以延长使用寿命,它有一个与封装焊盘形状一样的I/O图案,每个焊盘的孔径和位置都非常精确。该制程可以使金属漏印板满足助焊剂在位置和数量控制方面的要求,助焊剂发配精度可达0.051mm,数量偏差为±5%。
另外在RFS下方还固定有定位销钉用来对引脚框组件定位,这样可以减少定位中的误差累积,确保助焊剂发配时每个封装的位置精确一致。Capton黏着载带会阻碍丝印助焊剂,此时可在RFS下方做一些释放装置以适用于升高后的载带。
为适应EEMS封装的特殊要求,RFS每个I/O孔周围都加工有“环形”圈,以消除封装中凹陷型焊盘可能存在的助焊剂桥接风险。另外RFS内置的间隙高度可使助焊剂尽可能靠近焊盘表面进行印刷,进一步提高助焊剂数量和发配的精度。
◆焊球放置
与助焊剂发配需要很高精度一样的道理,焊球贴放也需要同样的精度。因此,RVSI也将其最新开发的技术配备在焊球贴放系统上,这是用在钻孔焊球光罩(DBM)中。和RFS一样,DBM也是由铝合金制成并具有与封装匹配的I/O图形,为焊球的精确贴放提供保証。RFS和DBM都有固定在焊球面对引脚框进行定位的定位销,这样更换工具时无需再作调整,减少转换时间。DBM的刚性很大,所以用真空或空气在吸住松开焊球时它不会弯曲,确保焊球贴放的精确度和重覆性达到最高。另外DBM具有平滑的表面,可以避免焊球黏附在光罩中间,提高良率和设备运行时间。总而言之,试验显示了DBM的焊球贴放精度能达到42μm,可良好地控制在制程误差范围之内。
◆定位夹具
由于载带基板具有一定挠性,因此定位夹具淮确重覆地对每一个封装进行定位非常重要。为了实现淮确的助焊剂涂覆和焊球贴放,加工过程中载带表面的共面度应保持在0.051mm范围内。可使用配备专用真空孔(每个晶片对应一个)的硬不锈钢插入板,这些独立的真空孔确保在整个面上支撑引脚框组件,使助焊剂发配和焊球贴放作业都在一个平面上进行。可收缩定位销预先将封装组件对淮,使引脚框位置一致且重覆性高,同时将表面共面度维持在0.051mm范围内,保証了VAi 6300助焊剂发配和焊球贴放作业所需的淮确度。
◆元件传输
为了防止封装中极易损坏的晶片受到损伤,在整个焊球贴放系统和材料输送设备中都使用边缘传送带。这种传送带仅与引脚框组件的边缘相接触,不会碰到晶片,但是回流焊炉和清洗机却都是用不锈钢网传送带,可能会导致部件损坏。为了避免这种危险,VAi 180使用一种传输线导引器将引脚框组件从焊球贴放设备移到回流焊炉的传送网上。导引器在五种流程中选择一个,将引脚框组件从VAi 6300送到选中的回流焊炉传送带上,并使传送网的速度与组件移到回流焊炉的速度相同,完成无缝无碰撞传输,避免了传送网与裸晶片之间产生有害碰撞的可能性。
本文结论
2000年5月,焊球贴装线已被整合到生产线中并进入全面生产阶段,转包商可用它对客户提供当今先进CSP的最新组装产品。EEMS使用的μBGA焊球贴放制程良率超过99.9%,虽然该制程对助焊剂发配、焊球贴放、定位夹具和材料输送带来了许多难题,但在客户和供应商之间的共同努力下已经找到了解决的办法,最终得到超出客户期望同时也使制造能力增强的制程方法。
深圳宏力捷推荐服务:PCB设计打样 | PCB抄板打样 | PCB打样&批量生产 | PCBA代工代料
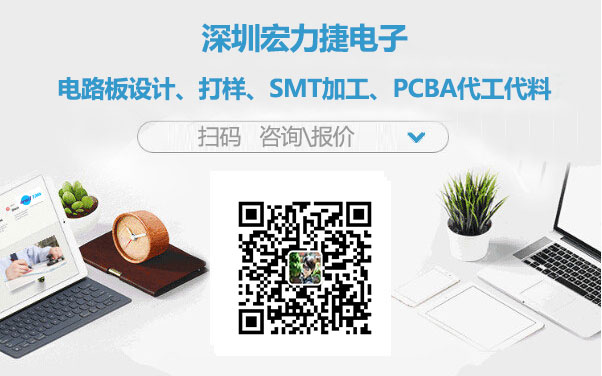