随着电子产品的设计与应用日趋复杂,整合的处理器、存储器等关键元件在性能规格上大幅提升,在考验承载电子零件的
电路板设计技术层次,不仅须在小面积达到高密度、高功效要求,也必须能具备良好电性、安全性与更严苛的使用条件…
近年来智能手机、平板电脑成为驱动电脑科技持续优化的重要产品项目,不仅产品越做越薄、越轻,功能不减甚至在性能、储存容量、产品电池续航力每每都能爆发一倍、甚至数倍的性能升级,其中除了半导体科技在3D IC与高阶异质封装技术的整合功效外,另一方面则是因应新元件与更小体积、更狭窄机内空间挑战的PCB载板技术能力升级。
电路板影响电子产业甚钜
其实早在出现印刷电路板之前,电子产品的零组件与电路建构,大多是利用铜导线直接连接电子零件完成导通电路,建构整个可运行的电子产品系统。但这种方式建构的电子电路,一方面在制作线路与连接零组件需耗用大量人力与制作心力手工进行,线路与元件焊接很容易产生错误连线而造成元件或材料耗损,徒增制造与验证线路成本。
改良方案即使用电子电路板透过金属化学蚀刻线路制作电路,搭配钻孔提供电子元件更稳固的连接与固定,达到更好的线路连线品质、元件固定效果,同时在制作、验证甚至产品出货后的售服、检修都能提供更高品质的电路。
因为印刷电路板(PCB)担负承载大量电子零件、建构元件导通电路的关键角色,PCB也成为电子产品持续进化、升级的重要组件!PCB的线路制作主要分成两种作法,基本上PCB本身必须具备一绝缘载板,载板材料即决定了PCB电路板本身的强度、绝缘效果、基本电性表现,而导通线路可以用加成法(Additive)或是减去法(Subtractive)两种不同制作方式建构。
软板?硬板使用条件优势不同
线路加成法为透过在基板上进行实体电路的金属电镀、蒸镀或是导通材料加成制成;减去法则是采在已覆盖金属导体层的基板上,搭配印刷线路图案后再将无印刷的无线路区块金属透过化学溶剂腐蚀去除形成电路。
早期基板材料一度成为限制电路板应用的瓶颈,随着兼顾如可挠性的软性材料、高温耐受性、兼具薄化与多层堆迭应用的各式机板材料相继推出,其中在高单价的软性或可挠式电路板多使用如加成法处理线路,而硬式电路板或多层电路板多数状况会使用减去法制作线路,软性(可挠性)电路板与硬式电路板因为适用环境与材料特点不同,其中以硬式电路板用量大许多,也发展出更精密的多层板、高密度多层板等进阶产品,对于薄化、缩小化或轻量化电子产品的设计目标上成为相当关键的核心材料技术。
从单层到双层甚至多层 考验制造与化学处理精密度
一般基材的导通层(电路)建构,可设置于基板的上、下两面,透过钻孔与孔内线路电镀贯穿孔的方式形成上下电路线路的连结导通线路,随着电子产品产业对高精密度、高复杂度整合电路的需求,也形成多片硬式电路板堆迭、搭配电路层与层间的导通连接与黏合设计,建构线路更趋复杂的多层板结构。
多层电路板可有效简化基板尺寸、面积,尤其搭配IC科技的高度整合元件,电路载板甚至可以缩减传统线路的数倍到数十倍之谱,成为电子产品积极缩小优化的关键设计趋势。
多层板、高密度电路板的整合设计不仅在制品技术远高于常规电路板,在产品利润也超过常规产品甚多,但随之而来的问题也相对更多,例如,多层板因为板材本身材料特性,在电子产品运行产生的温度也会导致板材热涨冷缩,对于高密度电路与层间导通连接的线路如果连接结构脆弱,也可能因为产品运行温度较高导致线路出现断路或是导通状态不正常问题。
因此高密度多层板虽然具备高利润、高材料集积缩小化优势,但衍生的测试、验证工作会更繁复、要求更高,精密度与材料受温度的变化量,也需要透过基板材料优化,提供高稳定、具抗温度变化的特性表现,才能使终端电子产品更能达到设计需求。
金属层材料选择 影响电路电性
除基板的材料特性外,置于基板之上的金属层也是电路板整体表现的关键。
一般来说金属层的材料不同、成本差距极大,也会直接左右生产成本,而对应不同金属材料在可焊姓、抗腐蚀、抗磨损?插拔、电阻性、导热性等都有极大差异,实际应用并不是材料越贵越好,而是必须针对不同金属层使用需求选用合宜的金属材料处理线路。常见金属层有铜、锡、铅锡合金、锡铜合金等,锡厚度多为5~15μm,铅锡合金多数厚度为5~25μm。
目前的电路板,主要由线路、图面(Pattern)组成,一般线路与图面为一起制作,而基材的绝缘板材本身即建立起各层的绝缘电性(介电层(Dielectric)),各层载板为透过导通孔(Through hole/via)形成应用电路连接,一般来说,较大型的导通孔为设置需插件焊接的电子零组件,另电路板也会设置非导通孔来进行表面黏着电子元件的设置焊接。
末段制程搭配板材处理 提升电路板稳定与耐用度
复合板材本身,若因空气潮湿也容易因吸收湿气造成板材变异、变形,而变形过程可能让线路导线产生断裂或接触不良。为增加板材寿命,通常会在板材表面的未焊接面或是板材表面增加一层环氧树脂,或搭配丝印印刷元件名称、位置、该电路板的版本号码、出厂日期等参考资讯。
由于电路板上的铜面、导通金属面直接接触空气,极容易出现板材氧化、上锡不良或是氧化变型造成铜箔脱落等问题,一般电路板完成后在未上料的板材上,仍需在需吃锡的金属面增加一层防氧化的保护层,例如,以喷锡(Hot-Air Solder Leveling;HASL)、化学镍金化(Electroless Nickel/Immersion Gold;ENIG)、浸镀银(Immersion Ag;ImAg)、浸镀锡(Immersion Tin)或以有机保焊剂(Organic Solderability Preservatives;OSP)保护金属接点。
至于电路板成品验证方面,因为电路板制程关卡繁琐,为让制品更趋精良减少不良件数量,制程设备应定期保养与清洁,以维持稳定制作条件,生产也比须在高清洁度的环境下进行,避免成品出现误差。
板材处理为多道化学液浸泡、处理运作,设备必须维持自动定温、定时与定速处理料件,同时制程过程需随时视液料PH值添加化学品,维持化学浸料的成分稳定性。
除制程标淮化维持制品品质外,制品品质也必须靠高清洁度环境避免材料受污染,如生产线可在无尘环境下处理操作,液态光阻产线必须在搭配落尘过滤、板面除尘条件进行PCBA加工。
生产即密切关注各阶段处理 维持一贯品质、减少生产瑕疵
为维持后段工件的产出品质,在每个PCBA加工段的制程处理都不可忽视品质问题,过程出现瑕疵、最终制品品质也会大受影响。每段制程都需要实施首件制品检测、末件制品检测、及中间制品取样监测,以维持产品PCBA加工品质监管。
在钻孔制程段,可实施插销规(Pin-Guage)检测孔径状态,验证首件制品品质,电镀制程可用掌上型孔铜测厚仪检验镀铜的厚度状况,并搭配切片检视孔隙的铜密度与内层接合状况,确保镀孔品质。而在镀铜后的板件磨边处理、去除玻璃纤维、树脂、粉屑后,再搭配砂带机对铜面整平并除去铜瘤与凹陷问题。
同时大批量生产则搭配机器视觉辅助,辅以自动光学输送带进行工件检测,而多层板的层间对淮可采X-Ray检测搭配,确认对位精淮度。另自动光学检测可搭配原线路图稿进行比对分析,防止工件的固定断线、线路短路或线路缺口问题发生。
在防焊制程阶段的裸铜板在经过酸洗、刷磨、微蚀后,需去除铜面的氧化层与微铜粉、并增加铜箔面本身的粗糙度才能提升油墨防焊层的附着力,同时提升保护电路板能力。在印刷阶段可用目测检视油墨均匀度,在电路板烘烤后必须搭配膜厚计测量涂佈的油墨厚度。
在多层板压合阶段,关键在于温度与压力控制,要能达到最佳压合,可透过二段式处理搭配加长二段热压时程,即可强化板件硬度、平整性与铜箔的附着力。最终电路板成品验证,一般可以CAM Data输出,搭配自动治具软体建构生治具制作程式,透过治具快速检测挑选不良工件。
多层板成品可透过治具与验证程式快速筛选出不良品。
使用精密接点探针,可快速检测电路板的线路导通品质与状况。
多层板线路越做越复杂,除制程繁复,也增加成品验证的困难度。
电路基板尺寸变小、复杂度增高,必须搭配高阶测试设备进行各项电性检测,避免问题基板,以提升电子产品制造品质。
深圳宏力捷推荐服务:PCB设计打样 | PCB抄板打样 | PCB打样&批量生产 | PCBA代工代料
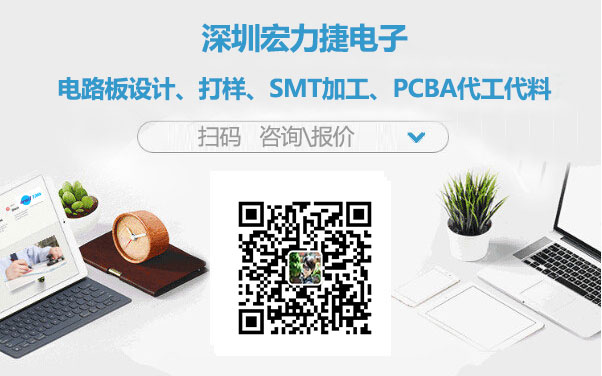