以代工为主的电子产品制造服务(EMS)环节的利润率越来越低,PCBA代工的质量保证要求却越来越高,根据SPC统计故障概率谱来设计工艺测试的工序点,借助一定的组装检测仪器设备来监控制程合适,是保证PCBA加工质量检测和改进提升的重要环节。对于许多中小型电子制造代工厂已无力投资增添高额成本的组装检测仪器设备,采用功能测试设计(Functional Tester Design)来保证PCBA加工品质,是一种性价比较高的措施手段,广泛应用于小批量多品种外协加工生产测试过程中。
1 引言
电子制造代工作为比较成熟的加工制造方式正在进入微利时代, PCBA代工的利润率是越来越低,PCBA代工的质量保证要求却越来越高。
在PCBA加工中的一个基本要求是一致性、正确性,对于差异要控制,变异不允许。在组装制造过程中的品质不良有设计问题、材料问题、组装问题三个方面,前两项需预先采取措施防止其发生,组装过程中的问题象缺件、损件、错件、偏移等大部分是可以目视检查的,但是焊接质量很难用目视的方法来完全判定,而且有时会出现PCBA交付在顾客处的炸机、爆板、功能不良等故障。
根据中国赛宝实验室可靠性研究分析中心提供的PCBA电装品质问题分析统计,主要的组装失效模式为焊接不良,占所有组装不良问题的57%,如图1所示。可见绝大多数产品品质问题是由组装焊接过程焊点故障引起的。
电装不良统计图
随着PCBA的设计趋于小型化,更小的器件,更小的间距,电子组装件的微型化(高密集度)越来越多,引起PCBA的焊点缺陷、检测定位困难、可视性及可维修性差,甚至不可修复潜在失效风险也随之增加。
仅从组装过程的传统目视检查控制不能完全剔除焊接不良,还需要进行自动X射线无损检测,在长三角、珠三角、还有军工生产中已经推广应用,效果十分好。但是增添设备的投资较大,本来劳动力成本连年递增已经让许多中小型电子制造代工厂叫苦不迭,再加上顾客对加工品质的不断要求,实力不强的代工厂已无力增添高额成本检测手段。
2 生产测试技术
目前在电子组装测试领域中使用的测试技术种类繁多,常用的有人工目视检查(Manual Visual Inspection,简称MVI)、在线测试(In-CircuitTester,简称 ICT)、自动光学测试(AutomaticOptical Inspection,简称 AOI)、自动 X 射线测试(AutomaticX-ray Inspection,简称AXI)、功能测试(Functional Tester,简称 FCT)等。
它们可以根据PCBA是否通过加电归为两大类:一种是电气测试技术,一种是非电气测试技术;也可以根据PCBA是否和测试设备接触分为两大类:一种是接触式测试技术,一种是非接触式测试技术。见表1,供参考。
2.1 人工目视MVI
人工目视测试是通过人的视觉比较来确认PCBA上的元器件贴装、插装、焊接质量。靠操作者的眼睛看或辅以放大镜、显微镜目视。这种技术是使用最久远和最广泛的在线测试方法之一,图1所示。
人工目视检查
但是随着微电子表面组装技术(SMT)的应用发展,电子产品朝轻薄小型化方向发展,印制板组件(PCBA)的密度随着元器件的不断微型化变得越来越高。密集插装元器件的相互阻挡视线,还有近几年广泛出现的微封装(0201) 、“不可见”焊点( 如BGA、 CSP 和倒装晶片组件FCA),人工目视“查颜观色”的方法肉眼已无能为力,已经无法保证PCBA加工的品质。
曾经有人进行过这样的试验,让四位经验丰富的检验员对同一块板子(中等复杂程度的线路板,如300个元件、3500个节点的单面板)的焊点质量分别作四次检验。结果是,第一位检验员查出了其中百分之四十四的缺陷,第二位检验员和第一位的结果有百分之二十八的一致性,第三位检验员和前二位有百分之十二的一致性,而第四位检验员和前三位只有百分之六的一致性。
这一试验暴露了人工目检的主观性,目检既不可靠也不经济。
目前在代工制造中,人工目视测试方法仅作为补充的辅助方法来使用。
2.2 在线测试ICT
在线测试仪(ICT),也称飞针(探针、针床)测试仪,图2所示。它的原理是通过对组装完成的PCBA在板元器件的电性能及电气连接进行测试来检查生产制造缺陷及元器件不良的一种测试技术手段。
一种ICT测试仪
在线测试仪测量时使用专门的飞针(探针、针床)与已焊接好的线路板上的元器件接触,并用数百毫伏电压和10毫安以内电流进行分立隔离测试,从而精确地测出所装电阻、电感、电容、二极管、三极管、可控硅、场效应管、集成块等通用和特殊元器件的漏装、错装、参数值偏差、焊点连焊、线路板开短路等故障,并将故障是哪个元件或开短路位于哪个点准确定位。
飞针测试最大的优点是市场反应速度快,但检测速度慢,适合测试样板和小批量订单。若是顾客要求打样品,可选择飞针测试,直到顾客做大批量订单时再改做针床测试,这样免去了顾客更改过程或撤销订单的针床制作成本投入。
ICT 的长处是电气缺陷测试,如器件的功能不正常或错值。在线测试能够有效地查找组装过程中发生的各种缺陷和故障,但它不能完整评估PCBA的电气性能。
ICT需要顾客的PCB设计符合ICT可测试性设计要求,对于代工顾客的的多样化层次实施起来较为麻烦。另外,PCBA测试的节点数越多,成本将急剧增长,主要是消耗在针床或飞针设计制造上,而且会存在下针测试困难的挑战。当节点数超过ICT的要求时,当PCBA的物理尺寸超过ICT要求时,问题将更难解决。
电子产品的小型化发展趋势直接导致了PCBA的设计微型化(高密集度) 组装,PCB设计对于ICT 测试节点仅留有很小的空间,甚至被取消,ICT测试的价值将随之消失。这就意味着生产制造将面临大量的潜在问题,PCBA加工完成直接进入终检,不仅会导致合格率的下降、返修量与故障诊断费用的增加,而且会造成生产的延误。
2.3 自动光学测试AOI
自动光学测试也称为自动视觉测试,图3所示。它的原理是机器通过摄像头自动扫描PCBA,将PCBA上元器件及焊接特征(贴片元器件状态、焊点形态及缺陷)捕捉成图像,通过软件处理,与数据库中合格的参数进行综合比较,判断这一元器件及其状态是否完好,然后得出检测结果。
AOI可以检查出PCBA上缺陷诸如锡膏印刷、元器件贴装(元器件缺失、极性反转)、回流焊接(桥接、或者焊点质量问题),并通过显示器或自动标志把缺陷显示/标示出来,供维修人员修理用。
AOI测试仪
这种测试技术是一种非电气的、无夹具的测试技术,对短路识别较差,不能检测电路错误,同时对不可见焊点的检测也无能为力。通常AOI工艺设计的SMT产线工序点有三处,锡膏印刷之后、回流焊前、回流焊后,如图4所示,可根据公司的具体需要选择。AOI测试的检测前置,起到的预防缺陷作用越明显。从总的使用效果来讲,AOI对SMT测试较好,对THT作用较差。
AOI技术的优势是对元器件贴装位置快速有效的测试。但是也有其不足和所面临的挑战:
(1)元器件的微型化
0402、0201甚至01005器件的逐步应用使焊点检测变得越来越困难。因为焊盘外露长度A在不断减小,甚至可能消失,这会造成器件定位不准及焊点不可检。如图4所示。
焊点不可检
(2)PCB的微型化(高密集度)
由于PCB设计的高密集度导致出现高矮器件相邻的阴影效应,小器件的一边焊点由于太靠近高器件,高器件挡住入射光而使这些焊点比较暗,如图5所示;二次反射光造成的偏色效应,小器件对称排放的间距小到一定值后,入射的红光(R)会使跟其对称的焊盘中间的红色偏多,如图6所示。AOI在测试这些焊点时会产生很多误报。
2.4 自动X射线测试AXI
X射线测试仪AXI如图7所示,组装好的PCBA沿导轨进入机器内部后,位于PCBA上方的X-Ray发射管发射X射线穿过线路板后被置于下方的探测器(一般为摄像机)接受,由于焊点中含有可以大量吸收X射线的锡铅金属元素,因此与穿过PCB玻璃纤维的X射线相比,照射在焊点上的X射线被大量吸收,而呈黑点产生良好图像,使得对焊点的分析变得相当直观,故简单的图像分析算法便可自动且可靠地检验焊点缺陷。X射线透视图可以显示焊点厚度,形状及质量的密度分布。这些指针能充分反映出焊点的焊接质量,包括开路、短路、孔、洞、内部气泡以及锡量不足,并能做到定量分析。
一种X射线测试仪AXI
X射线测试技术有两种方式,一种是2D或透射X射线测试法,这与简单的X射线胸透类似。对于单面PCBA焊点的测试,板上元器件的焊点可产生清晰的视像。另一种是断层或3D X射线测试法,目前PCBA制造商正在使用的、可实现3D X射线检验的技术被称作X射线断层照像机。X射线断层照像机之所以能够测试双面PCBA,因为它可以对两侧的焊点独立成像。还可对那些不可见焊点如BGA(BallGridArry,焊球陈列)等进行多层图像"切片"检测,即对BGA焊接连接处的顶部、中部和底部进行彻底检测。同进利用此方法还可测通孔(PTH)焊点,检查通孔中焊料是否充实,从而极大地提高焊点连接质量,避免过早失效。
这种测试技术是一种非电气的、无夹具的测试技术,一般设计工序放置点在焊接全部完成之后。AXI技术的优势是对焊接性能进行综合测试,避免焊点早期失效,提高品质可靠性,特别是对不可见焊点的检测。但不能测试电路电气性能方面的缺陷和故障,对于元器件的极性、方向测试能力不足,还面临开焊测试不能检出的挑战。
尽管ICT 和FCT 能够检测出封装器件引脚与焊盘间的电气连接是否有效,但这些技术却不能检验出品质低劣和/ 或可能产生过早失效的焊点。随着ICT的消失,取而代之可用AXI,保持较高的组装效率,并减少故障诊断与返修工作,使送到终检的PCBA良率大大提高。当然,由于AXI的价格昂贵,对于那些无力购置检测设备的厂家,可采用功能测试设计来弥补解决。
BGA焊点的3D X射线检测能显示出气孔和不充实的焊点
2.5 功能测试FCT
功能测试的基本原理是将组装完成的PCBA作为一个功能体,使其处于所构成的完整产品中,看其整机的所有功能和电气性能是否满足要求,藉此来评价PCBA的组装品质。对其提供输入信号,按照设计要求检测输出信号,包括电压、电流、波形等。这种测试是为了确保PCBA能否按照设计要求正常工作。
这种技术方法简单、投资可多可少,可以采用单片机控制设计成较为专业的自动功能测试仪,也可以自行设计成简易手动控制的专用功能测试仪。功能测试的缺点是不具有自动诊断故障和故障准确定位,只能确定故障的大致范围,维修还要靠技术分析和经验进行。
2.6 几种测试技术的比较
在电子组装行业,电子元器件及电子组件的微型化开始普及,微型的BGA、POP、01005,这个变化对组装工艺测试设计提出了挑战,特别是工艺测试设备(AOI、AXI、ICT)在测试的诸多方面遇到了挑战,如微型化(高密集度)PCBA给ICT夹具制造带来较大冲击,AOI设备的设计使其无法检测到藏于组件下面的引脚或焊接状况,BGA器件的引脚全部排放在器件底部,特别是对于带金属屏蔽的BGA,对于无引出线的多层电路板的BGA,使得ICT力所不能及等。此外,AOI、AXI这两种设备的测试还受到来料变化、焊点形态变化等影响,最终都会影响其检出率,不能很好地满足要求。
所以很难界定哪些技术手段是组装业所必须的,而哪些是不需要的,每种测试技术的应用领域和测试手段都不尽相同,都有其测试的侧重点,主要是根据工厂实力和承受能力来实施。从近几年的发展趋势来看,测试技术方法选择的主要依据应该着眼于PCBA组件和工艺的类型、故障概率谱和对产品可靠性的要求,使用两种或以上测试技术手段并用、互为补充乃是最佳途径。
各种组装测试的效能统计比较数据如表1,充分说明了不能靠单一的测试技术手段。
深圳宏力捷推荐服务:PCB设计打样 | PCB抄板打样 | PCB打样&批量生产 | PCBA代工代料
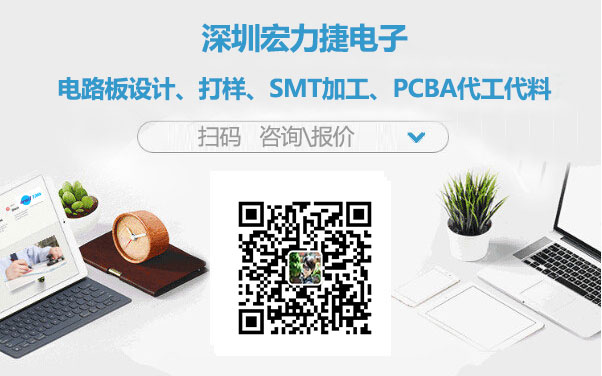