PCBA板加工是现代电子制造中的核心环节。它将元器件安装到印刷电路板(PCB)上,通过焊接和测试,形成具有特定功能的电子模块。由于PCBA板加工涉及多个步骤和工艺,因此需要遵循严格的规则以确保产品质量和生产效率。
以下是PCBA板加工过程中需遵循的一些关键规则:
一、设计规则
1. 设计优化:在开始PCBA加工之前,必须进行详细的电路设计和布局优化。设计者应考虑到元器件的布局、布线密度、焊盘大小、过孔设计等因素,以确保信号完整性和电磁兼容性。
2. 可制造性设计(DFM):设计必须符合可制造性原则,以简化生产流程,降低制造成本。应避免复杂的走线和狭小的焊盘,同时考虑元器件的可访问性和可维护性。
二、材料选择规则
1. PCB板材选择:根据产品的应用领域和工作环境,选择合适的PCB基材(如FR4、陶瓷、金属基材等)。同时考虑板材的厚度、层数和表面处理方式(如HASL、ENIG等),以满足电气性能和耐环境性的要求。
2. 元器件选择:元器件的选择应符合设计规格和可靠性要求,并确保其尺寸、引脚形状与PCB板上的焊盘匹配。此外,应选择具有良好可追溯性和稳定供货的供应商。
三、生产工艺规则
1. 焊膏印刷:焊膏印刷是SMT工艺的关键步骤。必须严格控制焊膏的厚度和分布,确保焊膏均匀覆盖焊盘。使用专业的网板和印刷机,定期检查和清洁网板,避免焊膏污染。
2. 元器件贴装:元器件贴装应采用高精度的贴片机,确保元器件准确放置在指定位置。对于不同类型的元器件,应调整贴装机的压力、速度和吸嘴,以避免元器件损坏或偏移。
3. 回流焊接:回流焊接是SMT加工的核心步骤。焊接温度曲线必须精确控制,确保所有焊点充分熔化并形成可靠的焊接连接。焊接后应检查焊点的质量,确保无虚焊、连焊、冷焊等缺陷。
4. 波峰焊接:对于DIP元器件,波峰焊接是常用工艺。必须确保焊接温度和速度的稳定,避免焊锡不足或过多。对于焊接后的板件,应进行目视检查或自动光学检测,确保焊点质量。
四、检测与质控规则
1. 光学检测(AOI):在贴装和焊接完成后,应通过AOI设备进行全面的光学检测,识别元器件的缺失、错贴、偏移、焊点缺陷等问题。AOI检测能够有效提高检测效率和精度,是确保产品质量的重要手段。
2. X射线检测:对于高密度BGA、CSP等封装元件,X射线检测能够检查焊点内部的连接质量,发现潜在的开路、短路、空洞等缺陷。特别是在检测双面PCB时,X射线检测能够提供更直观的内部结构分析。
3. 功能测试:在完成所有物理连接后,需进行功能测试,验证PCBA板的各项功能是否按设计要求正常工作。这包括电源测试、信号测试、通信测试等。功能测试能够及时发现并排除潜在的功能性问题。
五、环境控制与防护规则
1. 静电防护(ESD):在PCBA加工过程中,静电可能对敏感元器件造成不可逆的损坏。因此,必须在生产区域内严格执行静电防护措施,如佩戴防静电手环、使用防静电工作台和地垫,并控制空气湿度。
2. 清洁与包装:焊接和测试完成后,应对PCBA板进行清洁,去除助焊剂残留物,避免对电气性能的影响。包装时,应使用防潮、防静电包装材料,并在包装前检查PCBA板的外观和清洁度,确保产品在运输和储存过程中不受损坏。
六、质量管理规则
1. 全程质量监控:PCBA板加工的每个环节都需建立严格的质量监控流程,从原材料验收到成品出厂,都需经过多道质检工序,以确保产品的可靠性和一致性。
2. 持续改进:在PCBA板加工过程中,应定期评估和优化生产流程,采用新的工艺和技术,以提高生产效率、降低成本,同时提升产品的质量。
总结来说,PCBA板加工是一个高度复杂和精细的过程,涉及多个关键步骤和工艺。遵循上述加工规则,可以确保PCBA板的质量和可靠性,满足设计要求和行业标准。
深圳宏力捷电子是有着20余年PCBA加工经验的PCBA代工厂,工厂配备多条SMT生产线、DIP生产线,可提供从PCB设计、电路板制造、元件采购、组装、焊接、测试和最终交付成品电子产品的一站式PCBA代工代料服务。
深圳宏力捷推荐服务:PCB设计打样 | PCB抄板打样 | PCB打样&批量生产 | PCBA代工代料
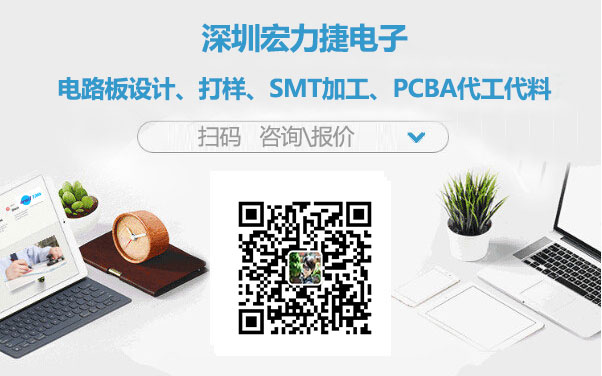