在智能手机主板生产线上,一块巴掌大的PCB板正以每秒5厘米的速度通过检测工位。3秒后,操作员老张的屏幕上弹出一条预警:BGA芯片位置的焊膏体积偏差12%。他立即暂停产线,调整钢网压力参数——这一幕发生在国内某电子代工厂的SPI检测环节,而类似的场景每天都在全球SMT车间重复上演。
一、SPI如何成为SMT产线的“火眼金睛”
SPI(Solder Paste Inspection)焊膏检测仪,这个看似普通的金属机箱里藏着精密的光学系统。不同于传统二维检测设备,其采用的激光三角测量技术可精确到±1μm的垂直分辨率,相当于能检测出人类头发丝1/70的厚度变化。当印刷完焊膏的PCB进入检测舱,高速扫描头会在0.8秒内完成对0402元件焊盘(0.5mm×0.25mm)的三维建模。
某军工电子企业的质量报告显示,引入SPI后,QFN封装元件的立碑缺陷率从3‰降至0.2‰。这种提升源于SPI对焊膏体积的精准控制——当检测到某个焊盘锡量不足时,系统会立即触发印刷机参数补偿,避免在回流焊后出现开路风险。
二、从救火到预防的质量管理革命
2018年某汽车电子厂商曾因ECU模块虚焊召回,事后分析根本原因是钢网堵塞导致的焊膏缺失。该事件后,行业开始全面普及SPI在线检测。现在的先进SPI系统已实现三大突破:
1. 动态公差补偿:根据元件类型自动匹配检测标准,如QFN器件要求焊膏厚度公差±15μm,而BGA则放宽至±25μm
2. 趋势预警机制:通过统计过程控制(SPC)分析,在参数超出2σ范围时提前预警,避免批量异常
3. 数据追溯系统:每块PCB的焊膏三维数据存档,可与后续AOI、X-ray检测结果交叉分析
某代工厂的实践表明,这种预防性检测使印刷工序的CPK值从1.0提升至1.67,意味着缺陷率从2700PPM降至64PPM。
三、隐藏的成本效益方程式
表面看,一台进口SPI设备需要80-150万元投资,但精明的生产管理者算的是另一笔账:以月产50万点的SMT线为例,SPI的引入可使:
- 贴片机抛料率降低40%
- 回流焊后维修工时减少65%
- 客户退货成本下降80%
更关键的是,SPI积累的焊膏印刷大数据,正在改变工艺优化模式。某企业通过分析12个月的历史数据,发现环境湿度每升高10%,焊膏扩散面积会增大3%。据此建立的补偿模型,使季节性质量波动降低了70%。
四、选择代工厂的隐形考核指标
当客户审核供应商时,除了关注贴片机品牌,更应考察SPI的应用深度。优质代工厂的SPI系统往往具备:
- 与MES系统实时联动的闭环控制
- 支持01005元件(0.4mm×0.2mm)的检测能力
- 可追溯3年以上的工艺参数数据库
某医疗设备制造商就因代工厂的SPI数据链不完整,在FDA审核时被开出483观察项。这警示我们:SPI不仅是检测工具,更是质量体系的重要数字基础设施。
在电子产品微型化趋势下,0201元件、0.35mm间距BGA已成为常态。当焊盘面积缩小到0.2mm²时,0.01mm³的焊膏偏差就可能导致焊接失效。SPI的存在,让SMT加工从经验主导的“手艺活”,进化成数据驱动的精密制造。它如同焊膏质量的基因检测仪,在元器件贴装前就剔除潜在缺陷,这正是现代电子制造走向零缺陷的必由之路。
深圳宏力捷推荐服务:PCB设计打样 | PCB抄板打样 | PCB打样&批量生产 | PCBA代工代料
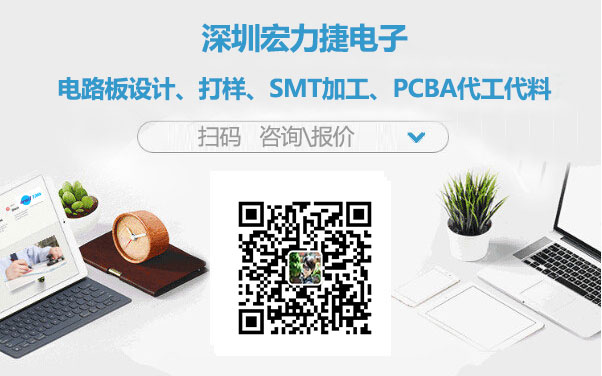