SMT表面安装技术在许多电子产品的生产制造中被大量采用,本文就SMT表面安装
PCB设计时需考虑的一些制造工艺性问题进行了阐述,给SMT设计人员提供一个参考。
关键词:印制电路板 基准标志 导通孔 波峰焊 再流焊 可测性设计
以前的电子产品,“插件+手焊”是PCB板的基本工艺过程,因而对PCB板的设计要求也十分单纯,随着SMT表面安装技术的引入,
PCBA制造工艺逐步溶于设计技术之中,对PCB板的设计要求就越来越苛刻,越来越需要统一化、规范化。产品开发人员在设计之初除了要考虑电路原理设计的可行性,同时还要统筹考虑PCB的设计和板上布局、工艺工序流程的先后次序及合理安排。本文结合作者多年的生产实践经验,对SMT表面安装PCB设计中的制造工艺性问题进行了总结,提出来供广大设计人员参考。
一、焊接方式与PCB整体设计
再流焊几乎适用于所有贴装元件的焊接,波峰焊则只适用于焊接矩形片状元件、圆柱形元器件、SOT等和较小的SOP(管脚数少于28、脚间距1mm以上)。
鉴于生产的可操作性,PCB整体设计尽可能按以下顺序优化:
(1)单面混装,即在PCB单面布放贴片元件或插装元件。
(2)两面贴装,PCB单面或两面均布放贴片元件。
(3)双面混装,PCB A面布放贴装元件和插装元件,B面布放适合于波峰焊的贴片元件。
根据上述推荐的PCB设计,以双面混装(如摄象机)为例,我们就可以设计如下生产工艺流程:
图1 双面混装PCB生产工艺流程
二、PCB基板的选用原则
装载SMD的基板,根据SMD的装载形式,对基板的性能要求有以下几点:
外观要求:基板外观应光滑平整,不可有翘曲或高低不平,基板表面不得出现裂纹,伤痕,锈斑等不良。
热膨胀系数的关系:表面贴装元件的组装形态会由于基板受热后的胀缩应力对元件产生影响,如果热膨胀系数的不同。这个应力会很大,造成元件接合部电极的剥离,降低产品的可靠性,一般元件尺寸小于3.2×1.6mm时,只遭受部分应力,尺寸大于3.2×1.6mm时,就必须注意这个问题。
导热系数的关系:贴装与基板上的集成电路等期间,工作时的热量主要通过基板给予扩散,在贴装电路密集,发热量大时,基板必须具有高的导热系数。
耐热性的关系:由于表面贴装工艺要求,一块基板至组装结束,可能会经过数次焊接过程,通常耐焊接热要达到260℃,10秒的要求。
铜箔的粘合强度:表面贴装元件的焊区比原来带引线元件的焊区要小,因此要求基板与铜箔具有良好的粘合强度,一般要达到1.5kg/cm2以上。
弯曲强度:基板贴装后,由其元件的质量和外力作用,会产生扰曲,这将给元件和接合点增加应力,或者使元件产生微裂,因此要求基板的抗弯强度要达到25kg/cm2以上。
电性能要求:由于电路传输速度的高速化、要求基板的介电常数,介电正切要小,同时随着布线密度的提高,基板的绝缘性能要达到规定的要求。
基板对清洗剂的反应,在溶液中浸渍5分钟,其表面不产生任何不良,并具有良好的冲裁性。基板的保存性与SMD的保管条件相同。
三、PCB外形及加工工艺的设计要求
PCB工艺夹持边:在SMT生产过程中以及插件过波峰焊的过程中,PCB应留出一定的边缘便于设备夹持。这个夹持边的范围应为5mm,在此范围内不允许布放元器件和焊盘。
定位孔设计:为了保证印制电路板能准确、牢固地放置在SMT表面安装设备的夹具上,需要设置一对定位孔定位孔的大小为5+0.1mm。为了定位迅速,其中一个孔可以设计成椭圆形状。在定位孔周围1mm范围内不能有元件。
PCB厚度:从0.5mm - 4mm,推荐采用1.6mm - 2mm。
PCB缺槽:印制电路板的一些边缘区域内不能有缺槽,以避免印制电路板定位或传感器检测时出现错误,具体位置会因设备的不同而有所变化。
拼板设计要求:对PCB的拼板格式有以下几点要求:
(1)拼板的尺寸不可太大,也不可太小,应以制造、装配和测试过程中便于加工,不产生较大变形为宜。
(2)拼板的工艺夹持边和安装工艺孔应由印制电路板的制造和安装工艺来确定。
(3)每块拼板上应设计有基准标志,让机器将每块拼板当作单板看待。
(4)拼板可采用邮票版或双面对刻V型槽的分离技术。在采用邮票版时,应注意搭边应均匀分布于每块拼板的四周,以避免焊接时由于印制电路板受力不均导致变形。在采用双面对刻的V形槽时,V形槽深度应控制在板厚的1/6 - 1/8左右。
(5)设计双面贴装不进行波峰焊的印制电路板时,可采用双数拼板正反面各半,两面图形按相同的排列方式可以提高设备利用率(在中、小批量生产条件下设备投资可减半),节约生产准备费用和时间。
PCB板的翘曲度。用于表面贴装的印制电路板,翘曲度一律要求小于0.0075mm/mm,具体如下:
表1 PCB容许的翘曲
四、PCB焊盘设计工艺要求
焊盘设计是PCB线路设计的极其关键部分,因为它确定了元器件在印制电路板上的焊接位置,而且对焊点的可靠性、焊接过程中可能出现的焊接缺陷、可清洗性、可测试性和检修量等起着显著作用。
阻焊膜设计时考虑的因素
(1)印制电路板上相应于各焊盘的阻焊膜的开口尺寸,其宽度和长度分别应比焊盘尺寸大0.05~0.25mm,具体情况视焊盘间距而定,目的是既要防止阻焊剂污染焊盘,又要避免焊膏印刷、焊接时的连印和连焊。
(2)阻焊膜的厚度不得大于焊盘的厚度
焊盘与印制导线
(1)减小印制导线连通焊盘处的宽度,除非手电荷容量、印制电路板加工极限等因素的限制,最大宽度应为0.4mm,或焊盘宽度的一半(以较小焊盘为准)。
(2)焊盘与较大面积的导电区如地、电源等平面相连时,应通过一长度较细的导电线路进行热隔离
(3)印制导线应避免呈一定角度与焊盘相连,只要可能,印制导线应从焊盘的长边的中心处与之相连。
导通孔布局
(1)避免在SMT表面安装焊盘以内,或在距SMT表面安装焊盘0.635mm以内设置导通孔。如无法避免,须用阻焊剂将焊料流失通道阻断。
(2)作为测试支撑导通孔,在设计布局时,需充分考虑不同直径的探针,进行自动在线测试时的最小间距。
对于同一个元件,凡是对称使用的焊盘(如片状电阻、电容、SOIC、QFP等),设计时应严格保持其全面的对称性,即焊盘图形的形状与尺寸应完全一致。以保证焊料熔融时,作用于元器件上所有焊点的表面张力能保持平衡(即其合力为零),以利于形成理想的焊点。
凡多引脚的元器件(如SOIC、QFP等),引脚焊盘之间的短接处不允许直通,应由焊盘加引出互连线之后再短接,以免产生桥接。另外还应尽量避免在其焊盘之间穿越互连线(特别是细间距的引脚器件)凡穿越相邻焊盘之间的互连线,必须用阻焊膜对其加以遮隔。
焊盘内不允许印有字符和图形标记,标志符号离焊盘边缘距离应大于0.5mm。凡无外引脚的器件的焊盘,其焊盘之间不允许有通孔,以保证清洗质量。
当采用波峰焊接工艺时,插引脚的通孔,一般比其引脚线径大0.05 - 0.3mm为宜,其焊盘的直径应大于孔径的3倍。
焊盘图形设计(见表2)
(1)片状元件焊盘图形设计
(2)SOP、QFP焊盘图形设计:SOP、QFP焊盘尺寸没有标准计算公式,所以焊盘图形的设计相对困难。引用松下公司的SOP、QFP焊盘图形设计标准参照执行,如表3所示。
表2 片状元件焊区尺寸
表3 SOP、QFP焊盘图形设计尺寸
深圳宏力捷推荐服务:PCB设计打样 | PCB抄板打样 | PCB打样&批量生产 | PCBA代工代料
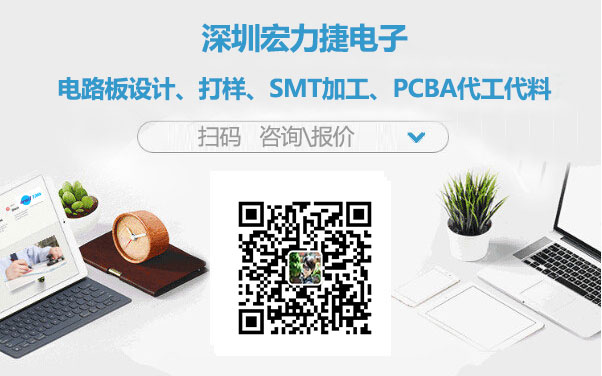