一般公司的新产品开发偶尔会遇到裸机高处落下的【冲击测试(drop test)】后发生
BGA锡球裂开的问题,如果RD有比较好的sense,就应该把产品拿去做一下应力应变分析,而
不是直接就把所有的BGA掉落问题都赖给PCBA制造工厂的SMT制程。
就深圳宏力捷的经验来看,BGA锡球裂开的问题其实很难仅靠工厂的制程管理与加强焊锡来得到全面改善,如果产品设计时RD可以多出一点力气,制造上就会省下很多的成本。
以下面这个案例来说,可以省下底材填充胶(Underfill)的材料费与工时费用,这还包含了间接管理与修复的费用,也可以提高产品的信赖度,更可以降低日后可能的市场商誉品质损失。
(BGA锡球开裂问题其实牵涉到很多的环节,「焊锡不良」只是其中一项而已,很多人一看焊锡开裂的第一个反应就是焊锡不良,但站在科学客观的角度来看问题时,只要看到焊锡的IMC有均匀的长成,基本上焊锡就没有太大的问题,再来就得探讨应力与焊锡强度的关系了,因为不论焊锡再如何加强,其承受应力的能力提升总是有限的,一定应力大于焊锡强度,焊锡破裂是可想而知的,所以在检讨完焊锡品质后,接下来就该检讨如何消除应力的来源与加强机构的抗应力设计了,本案例已经是先确认焊锡没有问题,所以才会要求RD加强机构设计来改善应力冲击。)
其实BGA锡球开裂的最大问题十有八九都来自于应力(Stress),不管是SMT回焊高温时板子弯曲变形所形成的应力,还是产品因为机构组装所形成的应力,或是因为客户使用时撞击,或不慎掉落地面所造成的外力,这些其实都是应力的来源,如果设计之初就可以模拟各种状况做应力应变分析,并针对可能产生应力的部份做一些设计调整以降低应力的影响,相信可以让BGA产品的生产品质更加稳定,甚至还可以移除一些不必要的underfill制程,达到节省成本的利益。
不知是否因为深圳宏力捷对新产品有过多次的类似要求,还是大家终于认识到设计影响制造的严重性,公司这次新产品的设计团队总算有个比较好的回应,也花了心思做了BGA锡球开裂的特性要因分析,发现应力的来源,并且做了设计变更来改善这个BGA锡球开裂的问题,当然有先用mockup的材料来做验证,结果也著实让人满意,事后实际修模生产后再做最终QA验证也都没有再发现BGA开裂的问题,真心希望这个「应力应变验证动作」以后会是RD验证的标淮程序。
利用应变计(Strain Gauge)验证机构设计变更前后对BGA锡球开裂位置的应变量分析
以下就是这款产品的大概设计外型与BGA所在位置,为了方便客户使用时不至于发生屏幕反光,所以产品设计了一个类似收银机的倾斜屏幕,也就是这个倾斜角让BGA零件在产品做正背面落下测试时承受了巨大的电路板变形量,以致造成BGA锡球裂开,因为产品的侧边(side)及角落(corner)摔落都没有发现问题,以前的例子几乎都是在角落摔出问题的。
既然知道可能的问题出在
电路板变形量过大,于是在电路板上黏贴【
应变计(Strain Gauge)】,所先量测未改善前的应变量数据,然后在电路板等主要组件不变得情况下,更换改善后的机构再做一次应变量的量测。
改善方法是在BGA零件的附近新增塑胶机沟肋柱(rib)来顶住电路板以降低电路板在落下时的变形量,参考上图的[New add rib]。
因为在做这个动作时产品的大部分设计都已经完成了,所以改善的方法就是尽量找到一个空间可以用来增加支撑柱,让电路板在落下变形时有硬物可以支撑住,以降低其变形量。
既然知道可能的问题出在电路板变形量过大,于是在电路板上黏贴应力计(Stress Gauge)然后先量测未改善前的应力数据。改善方法是在BGA的附近新增机沟肋柱(rib)来顶住电路板以降低电路板在落下时的变形量。
应变计量测机构改善前后的应变量
下表列出改善前与改善后(增加rib)的微应变量(Micro-Strain,x106)实际量测值。就如同预期的,在正面(倾斜面)落下时的应变量改善达到106,因为产品正面(Top)外型有个弯曲倾斜角,比较容易因为外力而造成弯曲;而背面(Bottom)为平面落下的应变量改善则比较小,只有42。
由此可见增加一根肋条(rib)就可以达到一定程度的电路板变形量改善。这个应变值量测的是电路板的Z方向,但是只有X轴的Z值,如果可以加测Y轴的Z值会更有参考价值。
|
改善前
|
改善后 |
改善量 |
正面落摔
|
-186 |
-80 |
106 |
背面落摔
|
203 |
161 |
42 |
这项设计变更执行后,经过DQ重新验证落下测试的效果,证实BGA没有再出现开裂的问题。
深圳宏力捷推荐服务:PCB设计打样 | PCB抄板打样 | PCB打样&批量生产 | PCBA代工代料
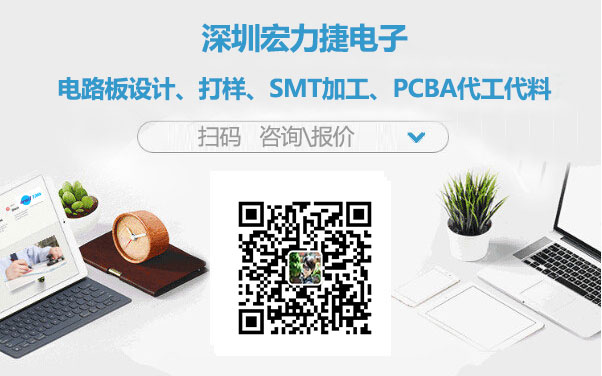